The Hydraulic Nut Clamps cover three basic sizes based on clamp force, Model 205 at 8,000 lbf, Model 200 at 10,000 lbf, and Model 201 at 15,000 lbf. The “Locked” designation (L) is added to the model number for the Locking screw that can be used to secure the clamp in position so Hydraulics can be removed during stamping. Locking clamps are commonly referred to as Hydra-Mechanical Clamps (HM) as they are hydraulically clamped and mechanically locked.
After selecting the model and Locking if desired, the clamp part number is built up based on the model number and then the clamping plate height or clamp height (CLH) and T-slot size. The clamping height is sized in ¼” increments for the small clamp heights and ½” increments above 2.00”. Note that these types of clamps are designed to clamp on a plate when close to the clamp plate. For varying clamp plate heights the clamp must be threaded up or down the threaded stud to achieve the starting clamp position close to the clamp plate and snug in the T-slot prior to clamping.
Fundamentally these clamps should not be adjusted in height without careful consideration of proper thread engagement in the Nut clamp and adequate stroke of the clamp to take up gaps between components. See the specific Nut Clamp User Guide and/or Specification Drawing for details on recommended gaps and heights.
For selecting the appropriate components to achieve catalog clamping height (CLH), PFA assumes standard JIC T-Slot dimensions to fit the T-Slot and typically Neck height is assumed as .750” for 5/8” slot, .875” for 3/4” slot, 1.000” for 1” slot.
| Model 200/200L | Model 201/201L | Model 205/205L |
Bolster/Ram Interface | T-Slot ¾” or 1” | Threaded Hole (TH) | T-Slot 1” only | T-Slot ⅝”, ¾” or 1” | Threaded Hole (TH) |
Clamping Force at 5,000 PSI | 10,000 lbs. | 15,000 lbs. | 8,000 lbs. |
Clamping Stroke | .29” | .60” | .25” |
Standard Thread Size | ¾” – 10 | Hole Size*** ⅝” – 11×1.85 minimum | 1” – 8 | ⅝” – 11 | Hole Size*** ½” – 13×1.85 minimum |
A | 2.50” | 3.12” | 2.00” |
B | Full Hydraulic (without lock) | 2.20” | 3.00” | 3.50” | 2.00” | 2.65” |
Hydra Mechanical (L) (with lock) | 3.20” | 4.00” | 4.90” | 3.00” | 3.65” |
D** | CLH* .50” .75” 1.00” 1.25” 1.50” 1.75” 2.00” 2.50” ** | No Lock 3.50” 3.50” 4.00” 4.00” 4.50” 4.50” 5.00” 5.50” ** | Lock (L) 4.00” 4.25” 4.50” 4.75” 5.00” 5.25” 5.50” 6.00” ** | No Lock 3.50” 3.75” 4.00” 4.25” 4.50” 4.75” 5.00” 5.50” ** | Lock (L) 4.50” 4.75” 5.00” 5.25” 5.50” 5.75” 6.00” 6.50” ** | No Lock 4.00” 4.25” 4.50” 4.75” 5.00” 5.25” 5.45” 5.95” ** | Lock (L) 6.00” 6.25” 6.50” 6.75” 7.00” 7.25” 7.50” 8.00” ** | No Lock 3.25” 3.25” 3.75” 3.75” 4.25” 4.25” 4.75” 5.25” ** | Lock (L) 3.75” 4.00” 4.25” 4.50” 4.75” 5.00” 5.25” 5.75” ** | No Lock 3.15” 3.40” 3.65” 3.90” 4.15” 4.40” 4.65” 5.15” ** | Lock (L) 4.15” 4.40” 4.65” 4.90” 5.15” 5.40” 5.65” 6.15” ** |
Weight | 3.0 lbs. | 5.0 lbs. | 8.5 lbs. | 2.0 lbs. | 3.0 lbs. |
| | 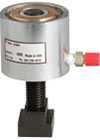 | 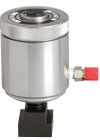 | 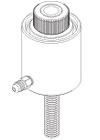 | 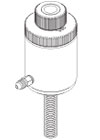 | 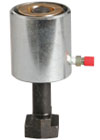 |  | 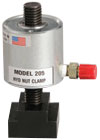 | 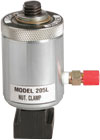 | 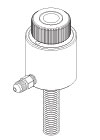 | 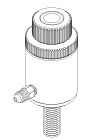 |
*Clamp Height (CLH) based on standard JIC T-Slot dimensions. T-Slot dimensions are typically: (Neck height is .750” for 5/8” slot, .875” for 3/4” slot, 1.000” for 1” slot).
**D=Product height installed is related to clamp height needed for clamp plate thickness. Stock sizes listed, but others are easily available. Dimension is worst case based on the smallest slot neck height and includes 1/4” clearance for slot variation.
***For TH models, threaded rod will engage bolster 1.3” minimum and range from 1.35” to 1.75” typical. If application is unique, call PFA for assistance.
Example: 13,000 lb. die typically uses a 15,000 lb. clamp such as Model 201. Clamp plate thickness (CLH) is 1.0”. 1” T-Slot.